





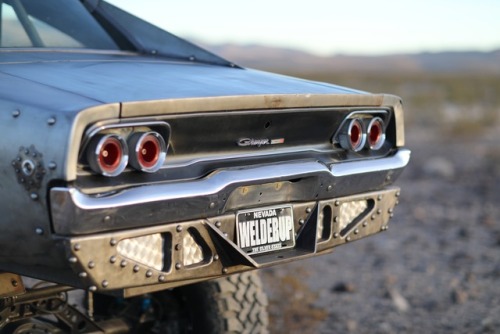
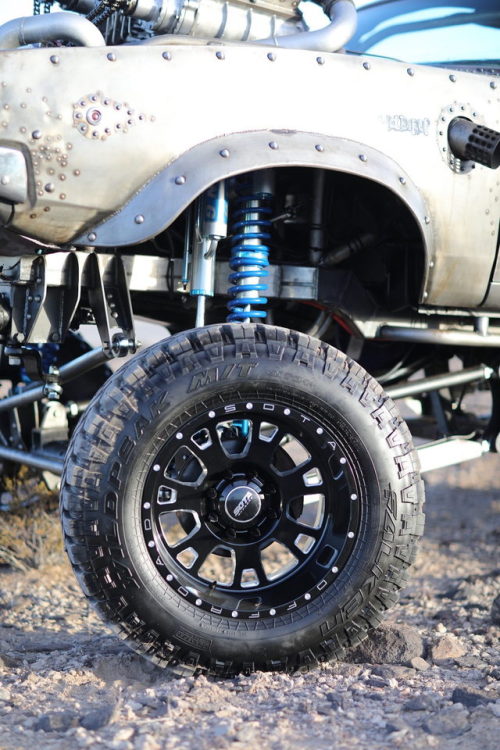
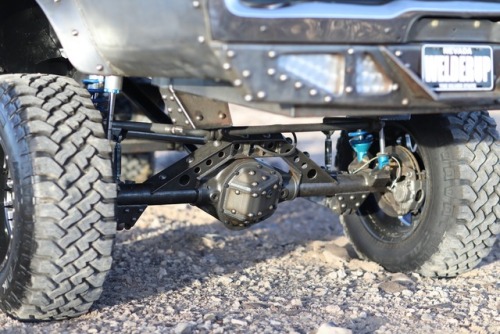
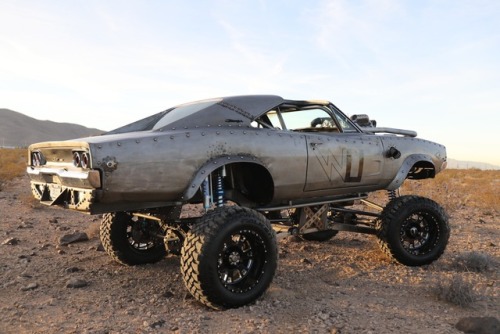
Dare To Be Diesel: WelderUp’s 4×4 1968 Dodge Charger!
For the final episode of their third season of Vegas Rat Rods, the crew at WelderUp whipped up a special creation that’s unlike any of their previous builds. WelderUp owner Steve Darnell was rummaging around with his friend Steve Peterson at his Peterson Boys salvage yard when they came across an abandoned project. It was a 1968 Charger, one of the most iconic muscle cars of all time. Still, that hadn’t stopped the previous owner from hacking up the wheel openings and cutting away swaths of the roof to add T-tops. Nevertheless, something did stop the previous owner before those removable roof sections ever came to be. The dented and cut up Charger spoke to Steve, “There was another Charger there that was a little more complete, but the fender flares and t-tops added character.” Steve thought about the possible directions the build could go, and a restoration was never an option. “I would have to replace every quarter panel and the roof skin. What part of the car would really be left?” Rather than replace virtually ever panel using aftermarket sheetmetal, Steve brought the car to his Las Vegas shop where he and his WelderUp crew spent five weeks turning the former 383-powered car into a ground-pounding diesel 4×4.
The Charger’s shell was in rough shape when it landed on Welderup’s doorstep. Once it was stripped bare, the car’s past meetings with other cars, bollards, and who knows what were spelled out in dents on just about every panel. Panels were peppered with holes from past dent repair attempts that were never complete. When WelderUp massaged the panels back into shape, Steve went back and filled the holes with some silicon bronze welding rod, leaving them proud of the sheetmetal like scars. That wasn’t quite enough though. The bare metal body needed a bit more to make it interesting, so Steve drilled the body for more than 200 rivets which were all welded from the back side.
Steve’s plan for the Charger called for big tires and an even bigger suspension, and that meant the unibody Charger would need significant reinforcement. A full frame was fabricated using 2×3-inch 0.120-wall steel tubing. A cage ties into the frame both in the cab and in the engine bay, completely encasing the engine and providing the upper mounting location for King coilovers and triple-bypass shocks. Those coilovers are attached to a Dana 60 front axle and a Dana 70 rear axle, both of which are mounted to the chassis with a four-link suspension and massive Heim joints.
WelderUp is familiar with diesel powerplants, but this one is even more extravagant than usual. Like many of WelderUp’s projects, the venerable 5.9L Cummins 6BT was called upon to provide the starting point for a brutally powerful build. The Industrial Injection long-block uses a P7100 injection pump that draws from a FASS fuel system. In that regard, the Cummins is similar to just about any 6BT you’d find under the hood of your average mid-’90s Dodge Ram built with high performance in mind. “Average” wouldn’t cut it at WelderUp, but Steve had a remedy in mind. He and WelderUp fabricator Merlin Johnson had been tinkering with some intake manifolds for months before the Charger was ever in the works. After mocking up three or four concepts that the two debated on, they settled on the dual 6-71 supercharger “birdhouse” manifold that now sits on the engine. The WelderUp crew wanted this engine to be more symmetrical than the average inline-six Cummins, and the twin superchargers were just what the diesel called for.
Built from 3/8-inch aluminum plate, the birdhouse was machined true and topped with superchargers rebuilt by Mad Dog Blowers. The engine fires up easily and has boost from idle on up to redline as each of the two Phatshaft turbos from Industrial Injection are spooled up by three cylinders worth of exhaust pressure as a split exhaust manifold routes the spent gasses to one turbo on each side of the engine bay. Yes, that’s right, even the turbos are symmetrical, sort of. With all of the exhaust ports on one side, the split manifold sends half of the exhaust over the engine to feed the passenger-side turbo.
Like all of Steve’s builds, the goal of the Charger was to inspire. It’s proof that something unique and cool can be built from truck parts and tossed-aside sheetmetal, and that not everything has to be fully polished or billet aluminum. With the right team working together it can even happen quickly, but it still takes a lot of effort, some personal risk, and more importantly the willingness to put a torch to metal and get the job done.
from Tumblr https://78.media.tumblr.com/4c12028d2e23ee1cfee7ed4c7a2fef4f/tumblr_p1pggqIGaI1vfi66so1_500.jpg